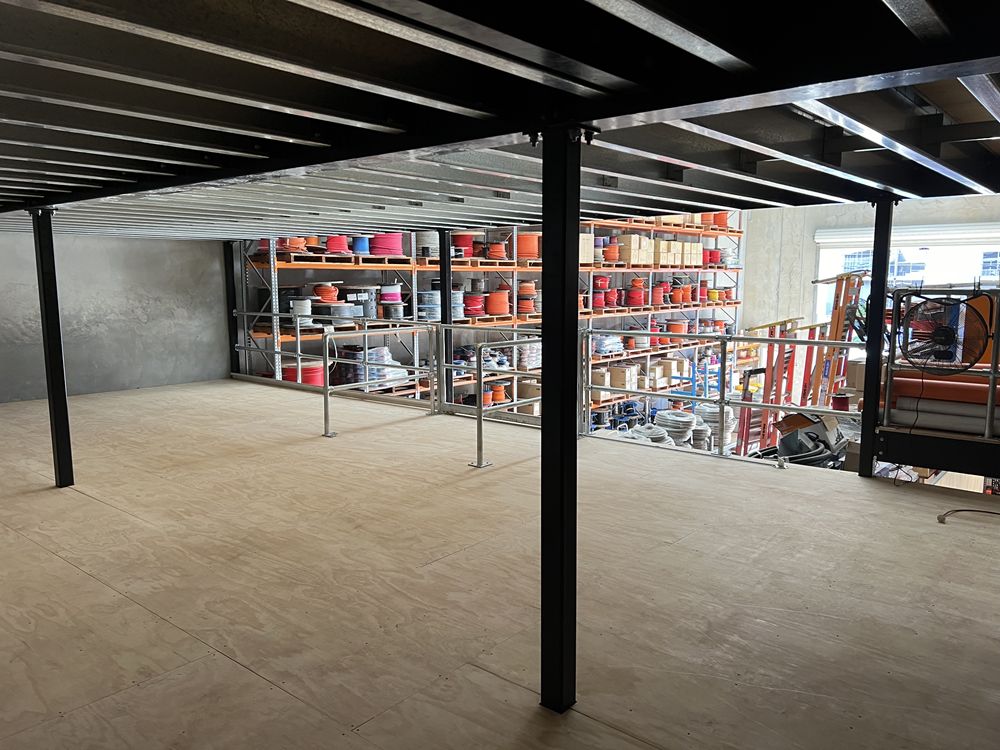
Multi-level mezzanine floors are an effective way to maximise unused vertical space in industrial environments. These structures transform empty airspace into functional work or storage areas, allowing businesses to grow within their existing footprints without the need for costly expansions or relocations.
Why Multi-Level Mezzanines Are Ideal for Industrial Spaces
Multi-level mezzanines offer numerous advantages in industrial settings, including:
- Space Efficiency: Multi-story structures optimise vertical space, providing additional storage, work areas, or equipment housing without the need to expand the building’s footprint.
- Cost Savings: Compared to the expenses associated with relocating or expanding facilities, installing a mezzanine floor is often a more budget-friendly option.
- Adaptability: Mezzanines can be customised to meet specific industry needs, whether for warehousing, manufacturing, or office spaces within industrial buildings.
Structural Requirements for Multi-Level Mezzanines
Designing and constructing multi-level mezzanines in Australia requires adherence to specific structural requirements to ensure safety, functionality, and compliance with national standards. Key considerations include:
1. Load-Bearing Capacity
- Structural Design Actions: According to AS 1170.1-2002, mezzanines must be engineered to support both dead loads (permanent static loads) and live loads (temporary or dynamic loads). For instance, light-duty mezzanine floors suitable for office use should support up to 350 kg per square metre, while heavy-duty floors for storage or industrial use should support at least 500 kg per square metre, with custom designs accommodating up to 1,000 kg per square metre or more.
- Load Combinations: Engineers must consider various load combinations, including environmental factors like wind and seismic activity, to ensure structural integrity under different conditions.
2. Material Selection
- Steel Structures: Utilising steel frames and reinforced flooring is essential for industrial applications requiring high load tolerance. Standards such as AS 4100 (Steel Structures) and AS 4600 (Cold-Formed Steel Structures) provide guidelines for the design and construction of steel components.
- Fire Resistance: Materials should meet fire resistance levels appropriate for the building type, as specified in the National Construction Code (NCC), to enhance safety.
3. Building Codes and Compliance
- National Construction Code (NCC): The NCC outlines requirements for structural integrity, fire safety, accessibility, and other critical aspects of building design. Mezzanine floors must comply with these provisions to ensure safety and legality.
- Australian Standards:
- AS 1657:2018: This standard covers the design, construction, and installation of fixed platforms, walkways, stairways, and ladders, specifying requirements such as tread heights not exceeding 190 mm, no more than 18 risers in a single stair flight, and balustrade heights no lower than 1 m with a 460 mm gap between the top and middle rails.
- AS 1428: Applicable to mezzanine floors exceeding 200 m², this standard focuses on design for access and mobility, ensuring accessibility for all users.
- Local Council Regulations: Compliance with local council regulations, including considerations of Gross Floor Area (GFA) and structural integrity standards, is crucial. Engaging with local authorities during the planning phase helps address specific requirements and obtain necessary approvals.
4. Accessibility and Safety Features
- Staircases and Handrails: Design must comply with AS 1657 or AS 1428, depending on the mezzanine size, ensuring appropriate tread heights, riser counts, and handrail specifications. Continuous handrails from ground to mezzanine level, with gaps not exceeding 125 mm, are required to prevent falls.
- Slip Resistance: Floor surfaces should have adequate slip resistance to prevent accidents, as assessed using the pendulum slip resistance tester specified in AS 4586:2013.
5. Fire Safety
- Fire-Rated Materials: Use materials that meet fire resistance levels appropriate for the building type.
- Smoke Detectors: Install smoke detectors above and below the mezzanine level, integrated into the existing fire alarm system.
- Emergency Exits: Provide clear and accessible emergency exits, with unobstructed paths of travel.
Adhering to these structural requirements and standards is essential for the safe and legal construction of multi-level mezzanines in Australia. Engaging qualified professionals, such as structural engineers and certified installers, ensures that all aspects of the mezzanine design and construction meet the necessary criteria.
Real-World Applications of Multi-Level Mezzanines
Multi-level mezzanines are used in various industrial settings to improve efficiency and functionality:
- Warehouse Storage: High-density storage solutions are possible by adding multi-level mezzanines, which expand vertical storage capacity without occupying more floor space.
- Manufacturing Facilities: Mezzanines help optimise workflow by providing dedicated spaces for equipment or materials, improving production efficiency.
- Office and Operations: Many industrial facilities integrate mezzanines as office spaces, creating an effective use of vertical space for administrative functions.
Benefits of Choosing Factory Mezzanine Floors for Multi-Level Solutions
Factory Mezzanine Floors offers tailored solutions to help industrial facilities make the most of their space. Key advantages include:
- Customised Solutions: We provide a variety of design options, each tailored to fit specific industrial needs.
- Experienced Installation: Our professional installation team focusses on minimizing downtime and disruption to your operations.
- Compliance and Safety Focus: Our mezzanine floors meet all council and safety standards, ensuring a safe and compliant addition to your facility.
Multi-level mezzanine floors are a practical solution for industrial facilities looking to maximise their space efficiently. By transforming vertical space into functional areas, businesses can grow without the need for relocation. Consider Factory Mezzanine Floors for a custom mezzanine solution that meets your facility’s unique needs.
FROM FIRST CONTACT TO FINAL INSTALLATION
You’ll be amazed at how quickly it all comes together when you commission a Factory Mezzanine Floor
Ask us for a free site visitNext-level business benefits

Cheaper than moving
Factory Mezzanine Floors increase your storage space for less than you would pay to relocate. Plus, there’s no downtime.

Recoup your investment in <12 months*
The majority of clients quickly recover the modest price of their initial outlay quickly.

Cheaper than extending or renovating
While structural changes are disruptive and expensive, installing a mezzanine can be done quickly and cost-effectively.

Our mezzanines are fit to your factory
We design our mezzanines to your specification and needs.
Are you ready to take it up a level?
Phone 1300 998 883 or enter your details for a prompt response.